Industrial Parts Box Molding

- KCN
- Xiamen,Fujian,China
- 30 days
- 50000Pcs Per Month
Product specifications: customized parts
Color: customized pieces
Minimum order quantity: 100 pieces for customization
Product name: Precision plastic parts
Product Category: Plastic Parts
Material:ABS
Manufacturer (Origin): Xiamen, China
Implement quality standards: ISO9001
Industrial Parts Box Molding:
Product Name: | Industrial Parts Box | Products Material: | PP |
Shrinkage: | 1.005 | Mold Cavities: | 1 |
Application: | industry | Certification: | ISO9001-2015 |
Mold Life-Cycle: | 100, 000-500, 000 Shots | Multi Injection: | Single/Double/Multi Color |
Drawing Format: | .STP / .Step / .Igs /.Stl /.Dwg / .Pdf | Sample: | Available. One Cavity Sample Mold or 3D Printing |
Specification: | Customized | Delivery Date: | 20-30 Days |
The molding process of PP toolbox mainly includes the following steps:
1. Mixing and sucking: First, mix PP/HDPE raw materials with masterbatch and filler masterbatch in a certain proportion, and then suck them into the plasticizing section through the negative pressure of the hopper of the injection molding equipment or blow molding equipment. In this step, the raw material mixed particles are heated in the barrel to melt the material, reach a flowing state and have good plasticity.
2. Injection molding: The material melt enters the designated mold and is molded by demolding. In this process, the mold or die head is the key to reshaping the plastic. The injection molded product is usually three-dimensional, so the mold design is more complicated and the shrinkage problem needs to be considered.
3. Cooling: In addition to the runner gate for pouring raw materials, the injection mold also has a cooling water channel for cooling the raw material design. This step ensures the stability and quality of the product after molding.
4. Loading and stirring: According to product requirements, PP particles, ABS particles and masterbatches in different proportions are added to the injection molding machine through a pneumatic conveying device. The loading process may produce packaging waste, and the stirring process is carried out in a closed device, which will not produce dust, but will produce noise.
This process involves key steps such as the preparation, melting, injection into the mold, cooling and shaping of plastic raw materials, and finally forms the required PP tool box product. This process involves not only physical changes, but also chemical changes, especially during the heating and melting of raw materials, which requires precise control of temperature and time to ensure product quality and performance12.
Other Plastic Molding Products:
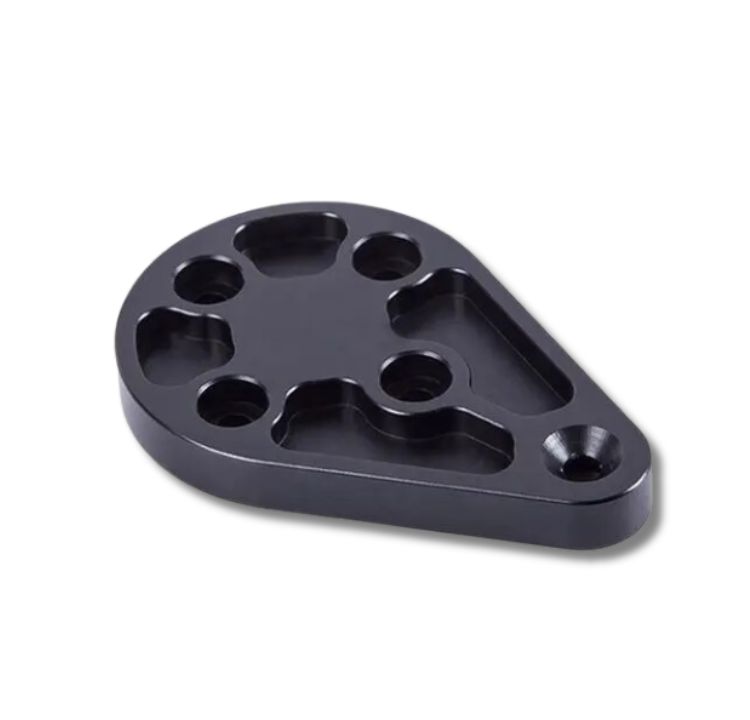
ABS Parts
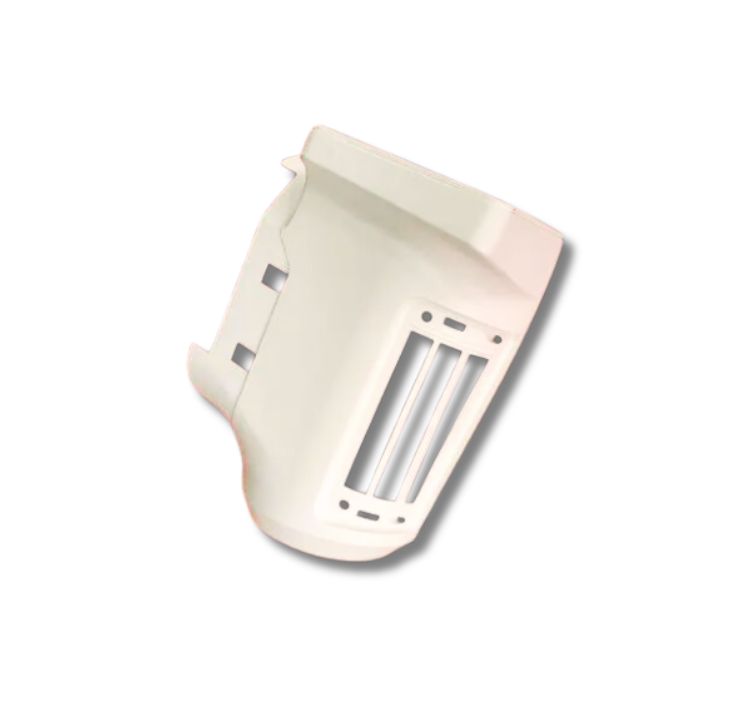
Appliance Housings
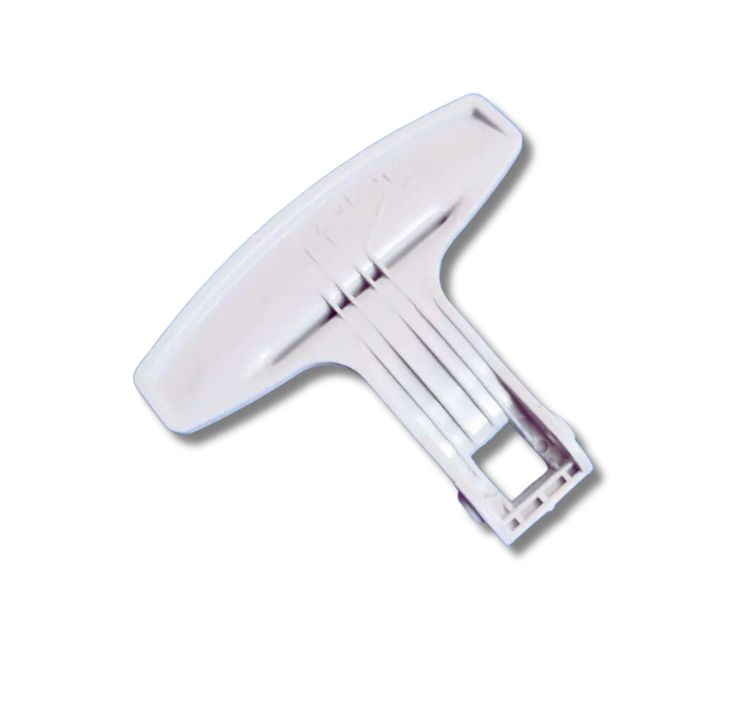
Electrical Parts
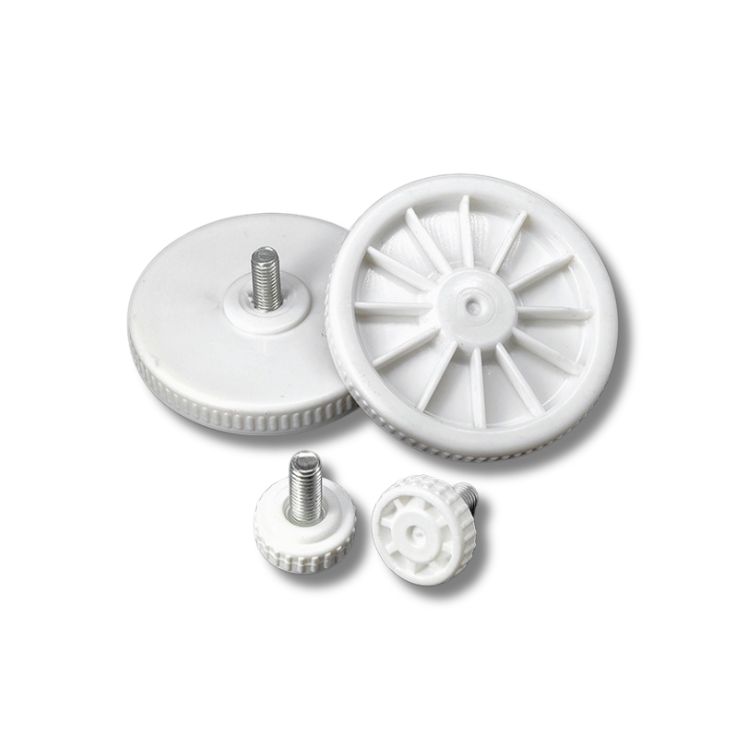
Overmolding